Rubber pool deck surfacing is a popular choice for many homeowners because of its durability, slip-resistance, and ease of maintenance. It is a flexible material that is easy to install and can be customized to fit the homeowner’s vision for the area. It is also a great option for those who want a softer surface for their pool deck. Rubber pool deck surfacing is available in a variety of colours, allowing homeowners to choose the perfect option for their outdoor space. Additionally, rubber pool deck surfacing is often less expensive than other materials, making it an affordable choice for many.
What is it?
Using similar methods to the surfacing applications found on playgrounds. Rubber surfacing can be applied over concrete to give a beautiful and safe finish. Rubber surfacing is poured onto the pool deck and typically worked with trowels to fit different shapes of pool decks. This system of pouring the rubber granules can be called many different names; Pour-in-Place Rubber Surfacing, Wet Pour Rubber Surfacing, Poured-in-Place Rubber Surfacing, along with other proprietary names. These are all referring to the same system of mixing polyurethane resins with synthetic granules. There are a wide variety of resins out there, which vary in purpose and chemical composition. Some are made to have softer and more elastic properties to them, while others may cure with durability and rigidity. Different binders and granules have benefits for different purposes, if it is paving, running tracks, playground surfacing, or other applications.
For pool deck surfacing, it is typical to see EPDM or TPV granules used for surfacing applications. EPDM and TPV are two types of rubber used in a variety of applications. EPDM is an ethylene-propylene-diene monomer rubber and is highly resistant to heat, ozone, and weathering. It also has good electrical properties, abrasion resistance and is tear-resistant. TPV is thermoplastic rubber and is a blend of rubber and thermoplastic polymers. It has excellent abrasion and tear resistance, as well as good low temperature properties. It is also highly resistant to oil and chemicals. Overall, EPDM is better for outdoor applications, due to its resistance to ozone and weathering, while TPV is better for indoor applications, due to its low temperature properties and resistance to oil and chemicals.
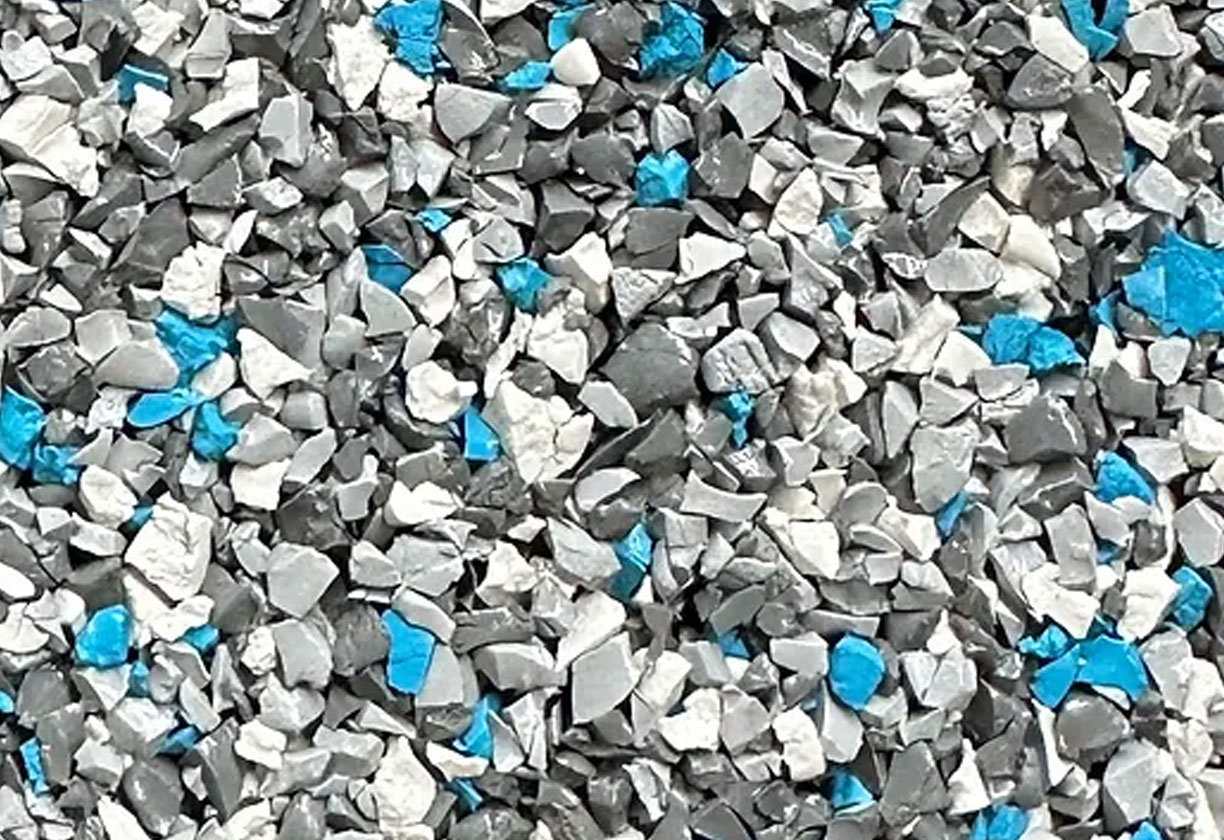
The EPDM or TPV granules can range in quality based on their tensile strength, hardness, density and polymer content. In the manufacturing process, there are different size granules that can be produced for different purposes. Often it is best to have a blend of granules sizes, this attributes to better interlocking surfaces. Depending on the properties in the granules, they will have better or worse longevity under different UV and wear conditions.
So why put rubber surfacing around your pool?
- Slip resistant
- Crack and shift resistant
- Aesthetics
- Long lasting
- Seamless
- Increase curb appeal
- Fast Installation times
- Economical
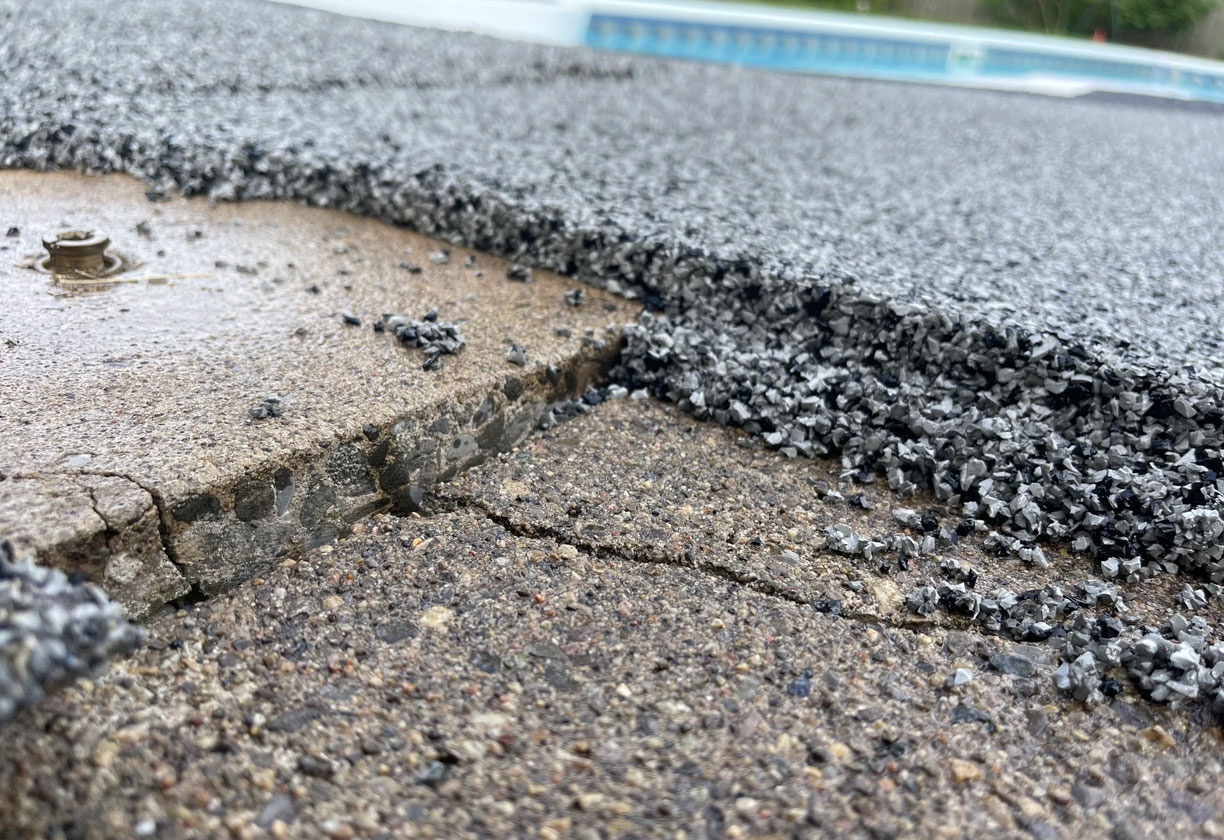
When kids are running around pool decks, every parent or grandparent has to keep an extra eye on them for safety. A little of the worry can be taken away with rubber surfacing applied on the pool deck. Having a softer landing for any trips and falls by the pool is always better than landing on hard concrete. With the seamless nature of the rubber surfacing, it removes the trip. The porous nature of the rubber surfacing helps with draining any standing water down to the underlying surface. This feature compared to a small puddle on stamped concrete for instance.
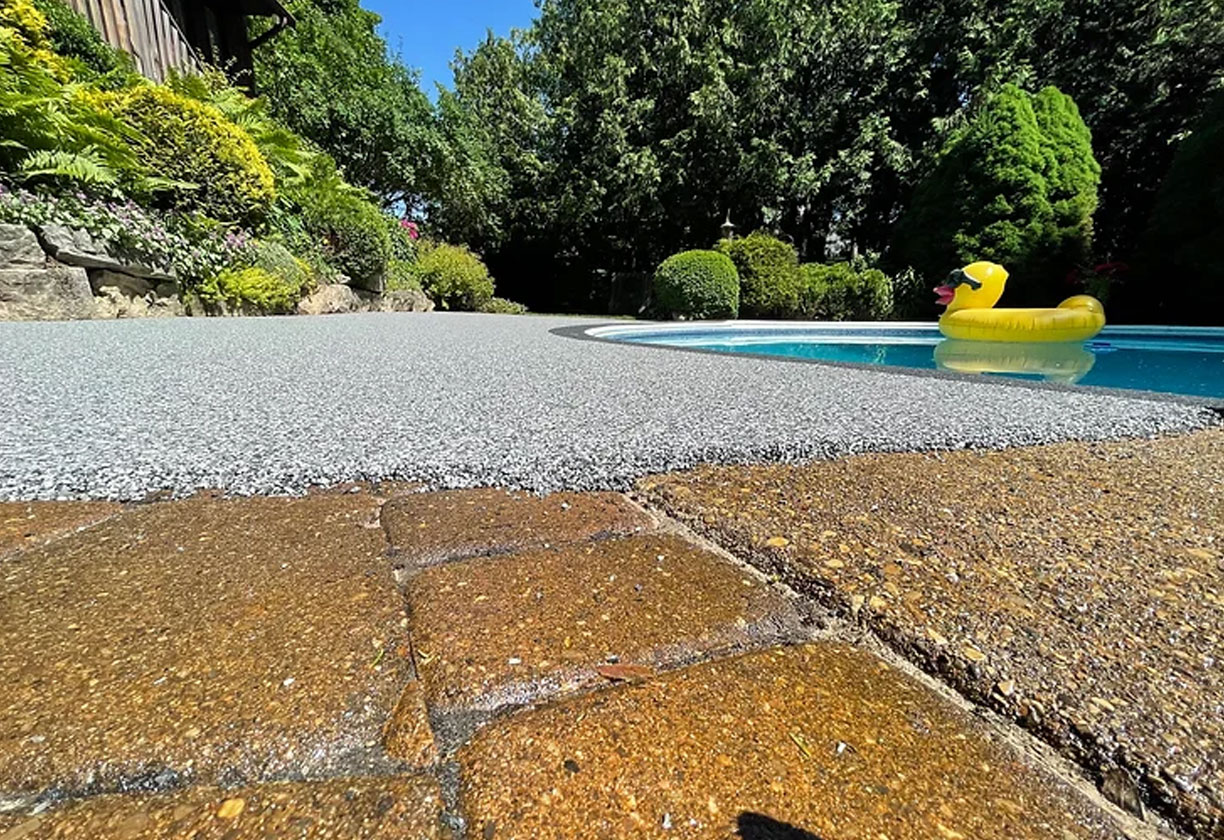
As an added feature, rubber surfacing can be applied to almost any surface. Easily covering common surfaces around a pool such as, stamped concrete, brushed concrete, exposed aggregate, interlock, wood decks and even certain types of tiles. There is of course recommended prep work depending on the environment and condition of the underlying surface. With this, the thickness of the rubber surfacing does matter depending on the nature of the project and the location. When looking at concrete that shifts around in winter months, it is good to go a bit thicker with the surfacing to allow more stretch instead of tearing. There are other techniques in prep work that can be done to reduce the risk of any tearing in the winter season. Making rubber surfacing is an extremely attractive product for many outdoor applications